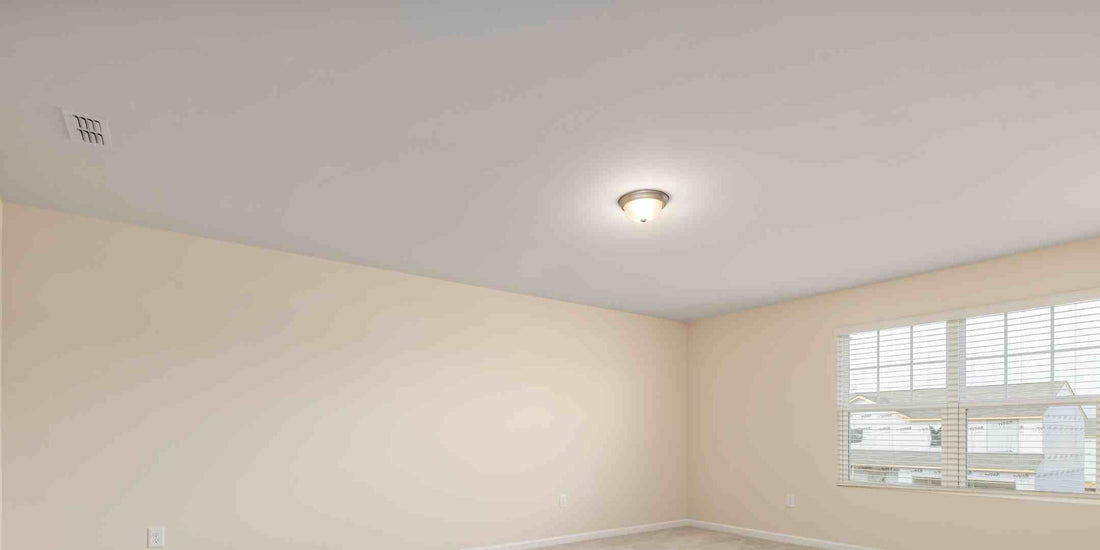
Hardiflex Ceiling Installation: A Step-by-Step Guide
Share
If you're tired of looking at a damaged or drooping ceiling, then it’s about time to change it.
Leaks and moisture can wreak havoc on ceilings, causing stains, sagging panels, and mold growth. Termites might chew through wooden ceiling materials, and traditional gypsum boards can crumble with persistent dampness or heat.
We're sure you don't want to be burdened with these issues. Our ultimate advice? Switch to Hardiflex.
Why? It’s built to handle those challenges. Made from a mix of cement, sand, and fibers, Hardiflex doesn’t rot or warp when exposed to humidity. It won’t serve as a snack for termites, and it doesn’t burn like wood. If you're convinced and want this material for your ceiling then we'll walk you through its installation method.
Let’s get started!
Tools and Materials You’ll Need
- Hardiflex boards – Typically 4.5mm thick panels are used for ceilings (standard size is 4×8ft).
- Metal furring channels (galvanized metal strips) or wooden joists create the support grid for the ceiling or the ceiling frame.
- Proper screws or nails for fiber cement.
- Hardiflex screws for metal framing, or galvanized nails if attaching to wood. (assure they’re the recommended type so they won’t rust or loosen.)
- Drill or screwdriver (preferably power drill)
- A circular saw with fiber cement. You can also use a score-and-snap knife for thin boards (score with a carbide blade and snap the board along the line).
- Measuring tape and pencil
- Level and Chalk Line
- Ladder or scaffold
- Dust mask (N-95 is better when cutting the boards (the dust has silica, which is harmful to inhale). You also need safety goggles for your eyes, and gloves to protect your hands. Hardiflex can be rough on the edges, and cutting it creates fine dust, so gear up.
It’s helpful to have everything on hand so you won’t shuffle in the middle of your project.
Hardiflex Installation Guide
1. Plan and Measure the Ceiling:
-
- First, inspect your current ceiling structure. Remove any old ceiling panels if present and make sure the area is clear.
- Measure the length and width of the room to figure out how many Hardiflex boards you’ll need. Always mark the walls where you want the new ceiling height or frame to attach (use a chalk line or pencil). If using metal furring, also mark where the support channels will go. Proper planning here will make the next steps much easier.
2. Install the Ceiling Framing:
-
- Set up the support structure that will hold the Hardiflex. Typically, this means installing metal furring channels (or wooden battens) across the ceiling.
- Attach the metal furring channels to the existing ceiling joists or concrete slab using appropriate anchors or screws. Space the channels about 16 to 24 inches (40–60 cm) apart in parallel lines.
Tip: Ensure each channel is level and aligned (use your level tool). You can also add cross-furring pieces perpendicular to the main channels to form a grid for extra support, especially in larger rooms. By the end of this step, you should have a sturdy frame grid ready to hold the boards.
3. Measure & Cut the Hardiflex Boards:
-
- Take your Hardiflex panels and measure out the pieces you need.
- Mark cutting lines on the boards with a pencil. It’s often best to cut boards so that joints (where boards meet) don’t all line up in one row. Stagger them like bricks for a stronger and nicer-looking result.
- Use your circular saw with the proper blade (or score with a knife and snap the board carefully). Support the board firmly while cutting to avoid breaks or cracks.
- After cutting, you can smooth any rough edges with a bit of sandpaper for a clean finish.
4. Attach the Hardiflex Boards to the Frame:
This step is easier with a helper: one person can hold the board in place (or use a makeshift support like a T-braceor panel lift), while the other drives in the screws.
-
- Start at one corner of the room or along one edge.
- Lift the first Hardiflex sheet against the frame. Leave a small gap (about 1/8 inch or ~3mm) between sheets when placing them side by side. This tiny gap allows for any expansion and helps prevent future buckling.
- Using your drill, drive screws through the Hardiflex into the metal furring or wood framing. Place screws about every 6–8 inches (15–20 cm) along each support, and a bit in from the edges of the board (about 1 inch from the edge) so the edges don’t crack.
- Drive the screws flush with the surface (not sticking out, but don’t countersink so deep that they break the board surface). If using nails on wood, similarly space them and be gentle to avoid cracking the cement board.
- Continue this process for each board, working your way across the ceiling. It’s often wise to attach the full boards first and then fill in smaller edge pieces last.
5. Secure and Check Your Work:
-
- As you attach each board, pause to ensure it’s sitting flat and the screws are secure. If you notice any board not fully flat against the frame, add an extra screw in the middle to pull it snugly.
- Make sure all screw or nail heads are flush with the Hardiflex (you don’t want bumps on your finished ceiling).
- Also, double-check that you haven’t missed any framing when screwing. It helps to mark on the board where the hidden metal furring lines are, so you hit them every time.
- When all boards are up, inspect the seams: the gaps between boards should be consistent (and remember, a small gap is intentional).
6. Finishing touches
-
- Tape and mud the joints just as you would for drywall.
- Apply joint compound (putty) to fill the gaps and cover the screw heads
- For a smooth finish, you can use fiber mesh tape or paper tape on the joints before overing them. This helps prevent cracks later.
- Scrape the compound flat with a putty knife and let it dry.
- Once dried up, sand the patches lightly until everything is smooth and level with the boards. Then apply a coat primer.
- Finally, paint your ceiling with your preferred color. Apply two coats at least for a good quality coverage.
Now that the ceiling is installed, let’s go over key pro tips to make sure your project is a success and review mistakes to avoid.
Here are some tips to help your Hardiflex ceiling installation go smoothly (and pitfalls you can steer clear of):
- Use a Dust Mask When Cutting: We can’t stress enough on this. Fiber cement releases fine silica dust. Wear an N-95 respirator mask (at minimum) when sawing or sanding Hardiflex. This dust is harmful to your lungs. Also, cut outdoors or with good ventilation if possible. Your future self (and your lungs) will thank you.
- Hardiflex is tough but brittle on the edges and corners. If you need to put a screw or nail close (within ~3/4 inch) to the edge of a board, drill a small pilot hole first. This prevents the board from cracking. Remember, fiber cement can crack under pressure, so easing the screw in with a pre-drilled hole helps keep the board intact.
- These boards can be heavy (a full 4x8 sheet can weigh a lot) and they don’t bend. When moving Hardiflex, carry it upright and with a friend’s help for large pieces. Support its middle to avoid stress on the center which can cause snaps or cracks. A cracked panel during installation is no fun. It’s easier to prevent breakage than to fix it.
- One common mistake is trying to span a big ceiling area without enough framing support, leading to sagging boards later. Follow the recommended spacing for your furring or joists (16–24″ apart). If the room is large, consider adding a couple of cross supports. This ensures your ceiling doesn’t wobble or flex. Essentially, the Hardiflex should always have support within about 2 feet or less.
- When installing multiple boards across a ceiling, don’t line up all the seams in one straight line. Stagger them (like a brick wall pattern). This makes the overall structure stronger and helps hide the joints, giving a more seamless appearance after painting.
-
Check for Power and Plumbing: Before drilling and screwing into an existing ceiling, be mindful of any electrical wires or plumbing pipes above. You don’t want to screw into a live wire or a pipe accidentally. If unsure, cut power at the breaker when working around electrical fixtures and proceed with caution. (This is more of a general safety tip, but very important!)
Installing a Hardiflex ceiling might seem intimidating at first, but as we’ve shown in this guide, it’s doable as a DIY project. With some careful planning, the right tools, and a free weekend, you can transform an old ceiling into a sturdy, attractive one.
Ready to get started? Gather your materials and give your ceiling the upgrade it deserves. You may drop by Wally's hardware to purchase your materials. Our hardiflex are of high-quality and in terms of its price, well we're sure it's competitive.
With Hardiflex above your head, you can rest easy under a ceiling that’s built to last. Happy installing and enjoy your new ceiling!